Overview
TPU (Thermoplastic polyurethane) is an elastomeric copolymer, made up of alternating soft and hard blocks, which give hardness and flexibility at the same time. This material is ideal for those applications where flexibility and durability are highly desired.
With Shore-A hardness of 98, TPU is a resistant material for several industrial applications, both mechanical or chemical. Moreover, it’s been especially designed to improve the 3D printing experience.
Compatibility: Find out the BCN3D printers and filaments compatibility
Applications
- Industrial seals, gaskets, sleeves or hinges
- Soft-touch multi-material models or handles
- Flexible-joined multi-material models
- Protective cases, Shoe soles, non-slip surfaces
- Springs, seals and shock absorbers
- Wheels and rollers


BCN3D Filaments
Industrial-grade materials manufactured by BASF and Mitsubishi Chemical and designed to deliver outstanding results for BCN3D printers.

Technical Information

Flexible with good wear resistance ideal for shock absorption
TPU is a thermoplastic elastomer, able to be extended up to 4.5 times its original size before breaking. Its exceptional elongation at break and strength make this material superior to most filaments.
How to Print
Printer Settings
![]() |
Extruder temp. 220° C - 260° C |
![]() |
Bed temp. 40° C |
![]() |
Cooling fan - |
![]() |
Speed 15-40mm/s |
![]() |
Min. layer height ≥0.1mm |
For BCN3D Stratos users:
Get a proper printing profile for TPU using the ones integrated into the BCN3D Stratos.
Bed adhesion:
To ensure good bed adhesion use Magigoo.
Recommendations:
- Store it in an airtight container with desiccant Dry filament before printing.
- Place it in an oven or in a dehydrator at 60-70ºC for 6 to 8 hours.
- Recommended sequencial printing: print one object at a time because travels leave residual material
Gallery

Flexible prototype validation
TPU makes manufacturing soft and functional prototypes possible to validate the comfort and the flexibility of the product.

Good corrosion and wear resistance
Its high oil and wear resistance and outstanding elongation at break make TPU ideal for testing functional and flexible prototypes.

Flexible end-use application
TPU is ideal for pipe connections or rigid systems as it absorbs vibrations, expansions and contractions to protect the components from the efforts derived from the operation of the equipment.

Roof upholstery protection tool
This tool is anchored to the upper pillar of the car when inserting the car floor carpet. The part protects the roof upholstery from any breakage caused by the insertion of the carpet. Without this tool, subsequent damage to the upholstery subsequently would entail a recovery job with many hours of rework would be required.
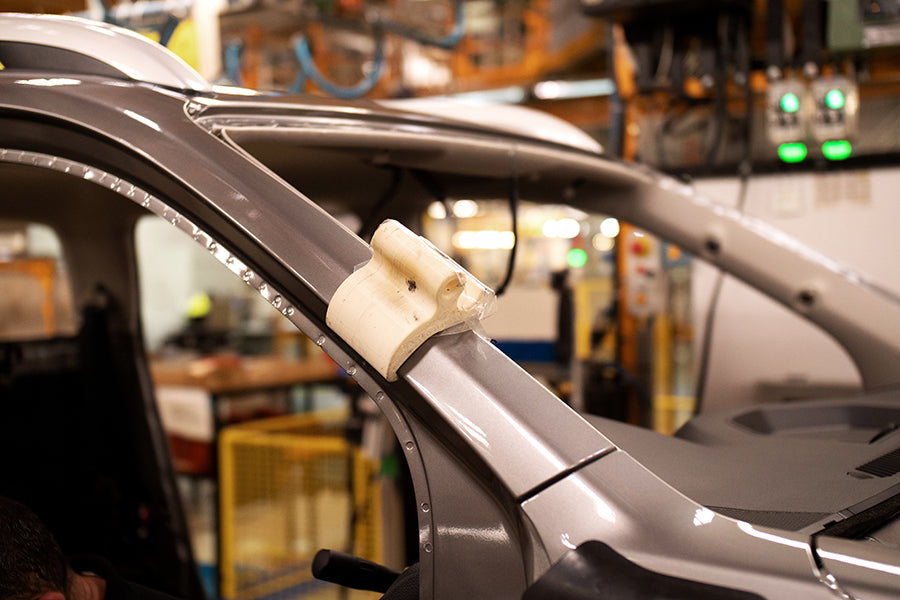
Windshield centring gauge fixture
This part functions as a gauge to ensure the correct distance between the A-pillar of the car and the windshield. Conveniently, the securing of the distance one side automatically secures the other.

Good corrosion and wear resistance
For Hyperloop CHF's subsonic train, the wheels are made from TPU for its strength, wear resistance, and ability to withstand high temperatures.

Product design prototype
While other rovers contain metal conveyor belts, the Clearwater team was looking for something more lightweight. In total, ¾ of the rover is 3D printed: the hulls in ABS for its toughness against sea conditions; ABS for the springs and bridge; TPU for the flexible, rubbery bristles; and PLA for some more rigid parts.